In 2019, the U.S. Department of Energy (DOE) took a big step toward improving energy efficiency by mandating that furnace manufacturers use efficient EC motors instead of traditional PSC motors in new units. This shift not only supports a more energy-efficient future but also helps to unburden the electrical grid.
With ECM motors, which were first introduced by GE back in 1985, the HVAC industry has seen a significant gain in popularity due to their ability to cut down on energy consumption, making them the next big upgrade in furnaces.
These motors will soon become the standard in all heating systems, replacing the old PSC motors in future models. The DOE estimates that this move will save as much as 3.99 quads of electricity and cut energy costs by over $9 billion by 2030.
However, furnaces manufactured before 2019 that still use PSC motors are still eligible to be sold and installed without any issues. For anyone looking to update their heating system, understanding the advantages of EC motors will make the transition to a more efficient, cost-effective future much easier.
What is an ECM Motor?
An ECM motor is a brushless DC motor that is designed to regulate the speed, torque, and power output without relying on external devices or sensors. Unlike the standard PSC (permanent split capacitor) motors, which only turn on and off at constant speeds, an electronically commutated motor can adjust its performance to meet varying demands. These motors differ by offering enhanced control and efficiency through built-in controls, making them a great choice for more dynamic applications.
How does an ECM Motor Work?
An ECM motor uses a microprocessor to control the motor’s speed and torque, ensuring steady airflow. These motors are factory programmed based on the HVAC equipment model in which they are installed, and cannot be programmed in the field. The manufacturer sets how the motor will operate, adjusting for applications requiring constant airflow or variable speed.
When increased torque is detected due to static pressure, the microprocessor increases the motor’s speed to maintain airflow. The system relies on a permanent magnet rotor, electromagnets, and coils in the stator. The controller sends power to energize specific coil sections, making the rotor spin in quick succession, drawing and rotating to maintain efficient performance.
Types of ECM Blower Motors
When you explore ECM blower motors, you’ll come across various types, each offering distinct advantages. These motors are designed to match different needs and improve the efficiency of HVAC systems. Let’s take a closer look at the types of ECM motors and how they perform in different conditions.
Constant Torque Motors
Constant Torque motors are designed to maintain a consistent level of torque even when the static pressure in the HVAC system changes. This is especially useful when airflow is restricted by dirty filters or clogged ducts. The key benefit of these motors is their ability to provide stable airflow despite the increase in pressure. Unlike PSC motors, ECM blower motors with constant torque ensure that performance is not compromised when the system faces challenges like air flow blockages or higher load demands.
Here’s how they work:
- They increase power to maintain the same torque when static pressure goes up.
- The motor is typically used in air handler blowers, and it can replace the older PSC motors.
- This type of motor is known to be more efficient and economical than other ECM motors.
- ECM motors with constant torque help maintain a steady airflow, even when systems face restrictions.
Variable Speed Motors
The variable speed motor is often referred to as a constant airflow motor or a constant CFM motor. It has the ability to maintain the same airflow despite changes in static pressure within the HVAC system. As pressure increases, the motor automatically adjusts by increasing both torque and speed, ensuring the airflow remains consistent.
Here’s what makes variable speed motors stand out:
- They are incredibly useful in high-efficiency furnaces and air conditioners, as they provide optimal performance under varying demands.
- Even when dirty air filters or high demand scenarios arise, these motors continue to work efficiently, maintaining airflow and system performance.
- True variable speed motors are different from constant torque or constant speed motors, as they can adapt seamlessly to changes in pressure and airflow needs.
Constant Speed Motors
A constant speed motor, also known as a constant RPM motor, maintains a fixed speed regardless of the changing static pressure in the HVAC system. If the airflow gets restricted, the motor increases torque to keep the system operating at the same pace.
Key characteristics of constant speed motors:
- Typically used for AC condenser fans, these motors are built to ensure consistent performance.
- They adjust the torque as needed to maintain speed when airflow is hindered.
- Ideal for situations where the motor needs to maintain a steady pace, even under restricted conditions.
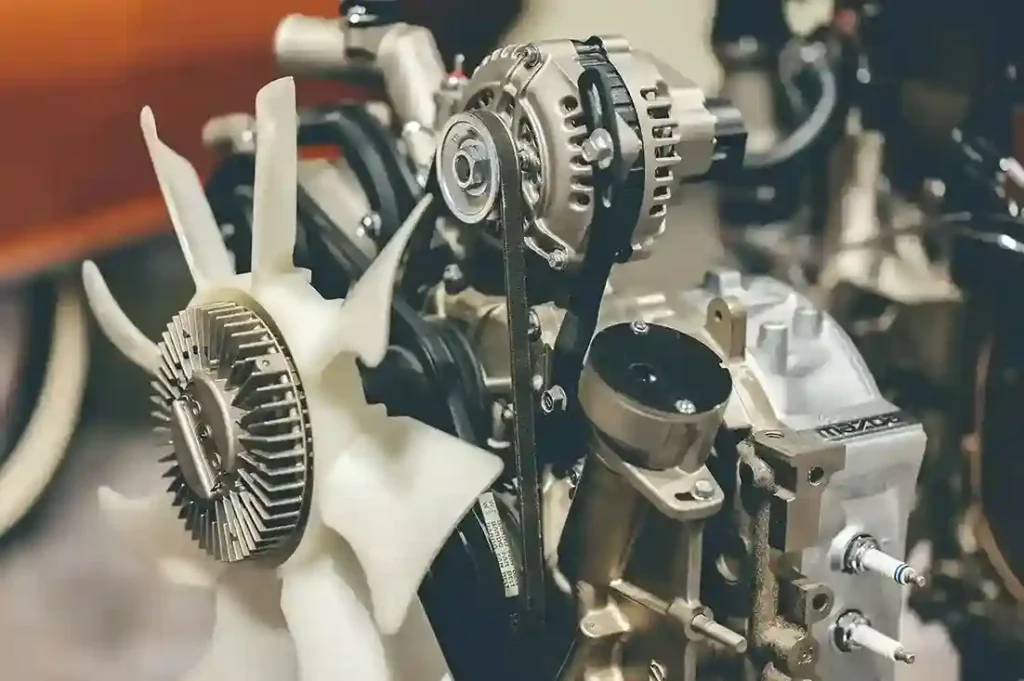
Advantages of an ECM Motor
ECM motors are highly favored in many applications due to their ability to enhance energy efficiency, reduce maintenance costs, and improve comfort and air quality. Below are some of the key advantages of ECM motors that make them stand out in the HVAC industry.
Energy Savings and Efficiency
One of the biggest benefits of ECM motors is their impressive energy-efficient performance. ECM motors operate at 65% to 75% efficiency, significantly outperforming traditional PSC motors, which offer only 45% efficiency.
This higher efficiency translates into lower energy costs, making them a smart investment for both residential and commercial settings. Not only does this save you money, but it also reduces your environmental footprint, contributing to sustainable energy use.
Variable Speeds for Better Performance
Another significant advantage of ECM motors is their ability to adjust variable speeds. These motors can easily vary their speed between zero and 100%, depending on the controller and the system’s needs. The speed adjustments are often permanently programmed or can be applied when the controller senses necessary adjustments.
This means that the motor can gradually increase or decrease speed in a smooth, energy-efficient way. For example, when the motor reaches a desired rate, it can gradually decrease to a soft stop, rather than an abrupt halt, ensuring smooth operation and saving energy in the process.
Lower Maintenance and Longer Lifespan
Maintenance costs are a concern with traditional motors, but ECM motors are designed to last longer and require less upkeep. Unlike regular motors, ECM motors are brushless, meaning there are no brushes to wear out or cause sparks. This eliminates the need for regular lubrication and reduces wear and tear on the motor.
Additionally, the gradual acceleration and deceleration of the motor mean less overheating, which extends its lifespan. On average, ECM motors can last up to 90,000 hours or approximately ten years of service, while PSC motors typically last only 50,000 hours or eight years. This makes ECM motors a more reliable and cost-effective solution in the long term.
Increased Comfort with Consistent Airflow
When it comes to maintaining a comfortable indoor environment, ECM motors excel. They are designed to run for longer cycles at lower outputs, which helps maintain consistent temperatures throughout the space. This prevents sharp increases or decreases in temperature, ensuring that your environment remains comfortable.
Additionally, ECM motors help to remove humidity and prevent temperature stratification, where warm and cool air layers form in different parts of the room. This contributes to a more pleasant, stable atmosphere for everyone.
Better Air Quality for Healthier Indoor Spaces
Finally, ECM motors play a vital role in improving air quality within indoor spaces. As HVAC systems filter household air during operation, the longer cycles of ECM motors ensure that air is filtered over extended periods, leading to cleaner, healthier indoor air. This helps reduce airborne pollutants and allergens, contributing to overall better air quality in your home or workplace.
Disadvantages of an ECM Motor
While ECM motors offer significant benefits over PSC motors, they also come with certain disadvantages that homeowners and technicians should consider. One of the top drawbacks is the cost.
For example, an ECM blower motor typically ranges from $600 to $1,500, which is considerably higher than a PSC blower motor, priced between $300 and $1,100, according to Home Guide. Another issue lies in the motor’s complexity, which increases the chances of something going wrong. If a part of the motor fails, the entire HVAC system will go down until the motor is either repaired or replaced.
Unfortunately, this issue cannot be easily bypassed to keep the system running. Furthermore, EC motors are programmed at the factory, making it impossible to simply switch out a faulty one with a new unit off the shelf. This leaves the system inoperable until a replacement is ordered, delivered, and installed, which can take a considerable amount of time.
ECM Motor vs PSC Motor Comparison
- PSC motors are simple alternating current motors that run at a constant speed, whereas ECM motors are more flexible and can adjust their speed and power output.
- PSC motors are single-speed and not programmable, while ECM motors offer programmability and can adjust to varying conditions.
- PSC motors have a chief advantage of affordability, but they are inefficient and consume more watts of electricity due to continuous energy consumption.
- ECM motors perform better than PSC motors in handling static pressure, as they can adjust power output, torque, and speed to suit different conditions.
- PSC motors tend to be noisier and are poor at managing humidity, whereas ECM motors are better at managing humidity and perform more efficiently in these environments.
- As static pressure increases, PSC motors experience a decrease in performance, whereas ECM motors maintain consistent performance under fluctuating pressure levels.
- PSC motors are less versatile in handling adjustable needs, while ECM motors excel in providing dynamic solutions for varying demands.
ECM Motor vs Variable Speed Motor
When we talk about the ECM motor, we’re diving into a motor type that can adjust its speed based on the static pressure of your HVAC system. In contrast, a variable speed motor is also designed to offer continuous and consistent airflow, but it’s primarily known for maintaining airflow and temperatures without much fluctuation.
The key difference? An ECM motor is specifically crafted to adapt to varying conditions, ensuring constant airflow and temperatures no matter the demands. Whether you’re aiming for energy efficiency or improved comfort, these motors are a great choice as they maintain the right balance automatically.
Upgrading to a Furnace with an ECM Blower Motor
When upgrading your HVAC system, it’s essential to consider the long-term benefits of an ECM motor. These energy-efficient motors help reduce energy costs by consuming substantial energy less than traditional blower motors. Not only do they enhance air quality and provide increased comfort, but they also offer longer lifespans and require lower maintenance, making them a wise investment for your home or business.
While the initial increased cost and the possibility of longer downtime during installation could be seen as disadvantages, the advantages of having an ECM motor far outweigh these concerns. Due to the DOE mandate for manufacturers to install ECM motors in new furnaces, consumers will soon have no option but to choose these high-performance motors, ensuring better comfort and efficiency in the long run.
FAQs
What is an ECM Motor and how does it work?
An ECM (Electronically Commutated Motor) is a type of motor that uses electronic controls to optimize its operation, providing energy efficiency and precise speed control. It works by using an integrated control board to adjust the motor’s speed based on demand, reducing energy consumption and improving overall performance.
What are the advantages of using ECM Motors over traditional motors?
ECM motors are more energy-efficient, as they adjust their speed to match the required load, reducing unnecessary energy consumption. They also provide smoother operation, lower noise levels, and a longer lifespan compared to traditional induction motors, which operate at a constant speed.
What industries use ECM Motors?
ECM motors are widely used in HVAC (Heating, Ventilation, and Air Conditioning) systems, appliances like washing machines and dishwashers, commercial refrigeration, and other applications requiring precise motor control, energy efficiency, and variable speed operation.
How do ECM Motors save energy?
ECM motors save energy by using an electronic control system that adjusts the motor’s speed based on load conditions. This ensures that the motor is running only as fast as needed, unlike traditional motors that run at full speed regardless of the demand.
Can ECM Motors replace traditional motors in existing systems?
Yes, ECM motors can often replace traditional motors in many systems. However, retrofitting may require additional components or modifications, and the compatibility depends on the specific application. Replacing a conventional motor with an ECM motor can result in significant energy savings and improved efficiency.